We are thrilled to bring you another exciting episode of the Offsite Construction Series featuring an amazing guest. Today, we have the pleasure of hosting Luke Haughton, the President of Sapphire, a leading company from the UK specializing in prefab balcony technologies.
Sapphire's Journey and Innovations: Company Background
Sapphire has been at the forefront of prefab balcony technologies, providing innovative solutions to the offsite construction market. Luke Haughton shares his background and the company's journey: Luke mentions, his uncle started the business 32 years ago, in 1992. They began as a provider of balustrades and handrails for staircases, offering stainless steel, glass, and hardwood handrails. By 2012, they were approached by a client who insisted they take on a project involving prefabricated balconies. Although it wasn't initially in their wheelhouse, this request led to the creation of our patented Glide-On Balcony system. "I joined the business when it was worth about $3 million. Over the past 10 years, we've expanded it to over $60 million. I've done everything from polishing stainless steel handrails in the early hours to managing projects and sales. Now, as the MD and president, it's been a rewarding journey seeing how client needs drive innovation and growth." said Luke.
Global Presence and Production Capabilities
Sapphire's reach extends beyond the UK, with a significant presence across Europe, the USA, Canada, and even New Zealand. They have nine factories worldwide and numerous storage facilities to manufacture and store products until they're needed on-site. Since launching the prefabricated balconies in 2012, they've completed over 40,000 units. While they currently have a factory in Toronto for North American projects, they strategically locate facilities based on logistical needs.
The Prefabrication Process: Design and Quality Assurance
Sapphire's start with thorough design work, transforming architects' concepts into manufacturable products. They have developed a quality app called Passport, available on the Google Play Store, which tracks every aspect of production and installation. This app provides complete traceability, from material certificates to installer sign-offs, ensuring high-quality standards. They created a counterbalance lifter to install balconies under overhangs without chain clashes. This flexibility allows them to work efficiently at any point on a building. The on-site support team offers specialized installer training, ensuring teams are well-prepared and maintain high standards. Depending on the market, Sapphire uses a combination of 2D and 3D designs to develop and refine concepts. This process includes detailed interface work, ensuring compatibility with different building types, such as concrete or mass timber.
Embracing Technology and Lean Manufacturing
The Passport App Sapphire's commitment to technology is evident in their in-house developed Passport app. Luke shares insights: "We designed the Passport app ourselves, and it has evolved to offer factory controls, site controls, and a customer-facing portal. Customers can track their project's progress with real-time updates and photos, much like tracking a Domino's pizza order. This transparency enhances trust and satisfaction."
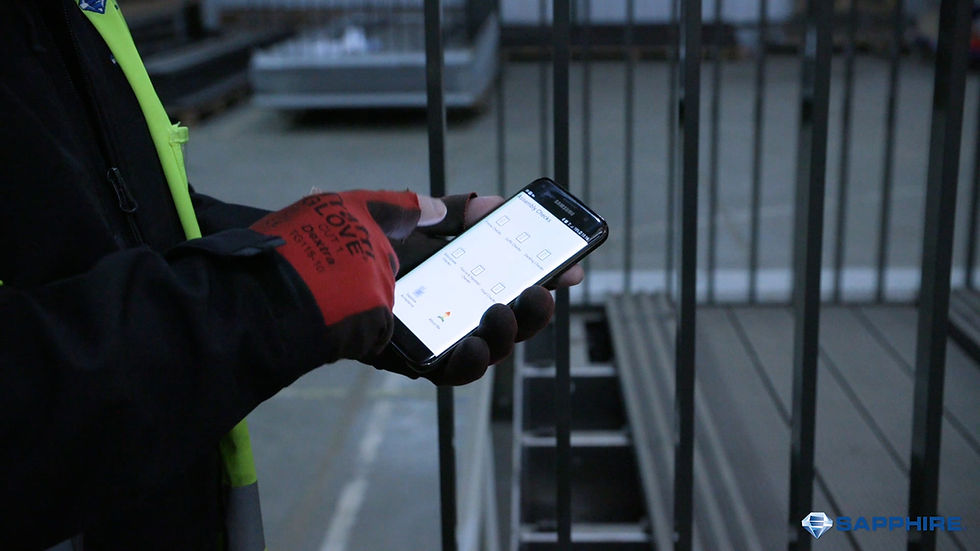
Record-Breaking Installations and Training Programs Installation Records
Their innovative approach has led to impressive installation records. The installers have set records, starting with 22 balconies in one day and reaching up to 62. These achievements are celebrated with trophies, motivating teams to excel. They work with a select number of teams in each market, providing training on our quality app and specialized equipment. Installers receive certifications and regular refreshers to maintain high performance.
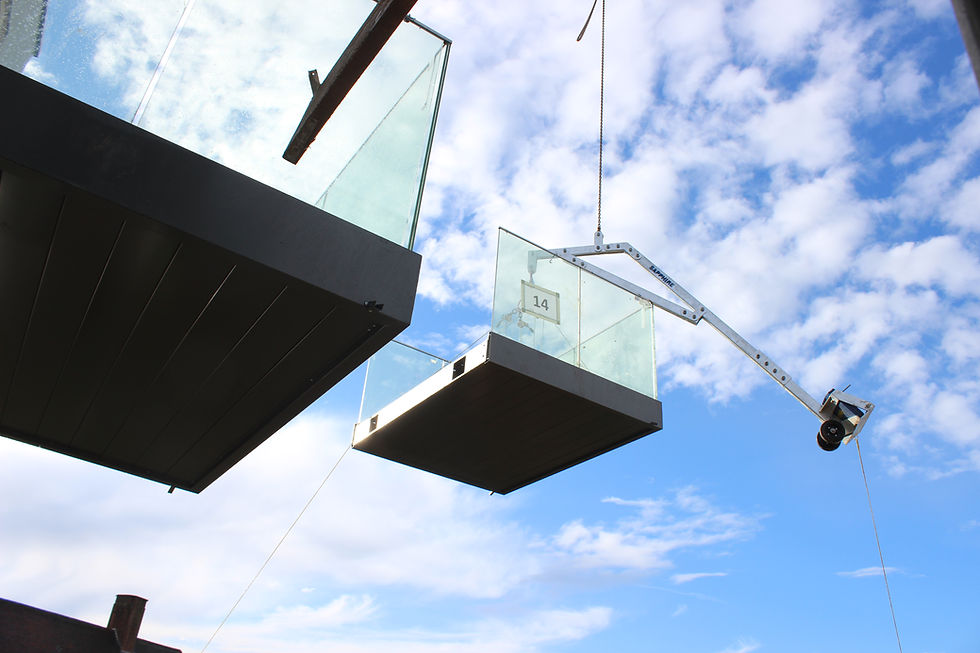
They have a new project in New York taking place this year. We will continue to keep in touch with this global company and look forward to seeing more projects here in the USA.
Comments